Sharing lessons to improve competence and capability in process safety - #HazardsAus2019
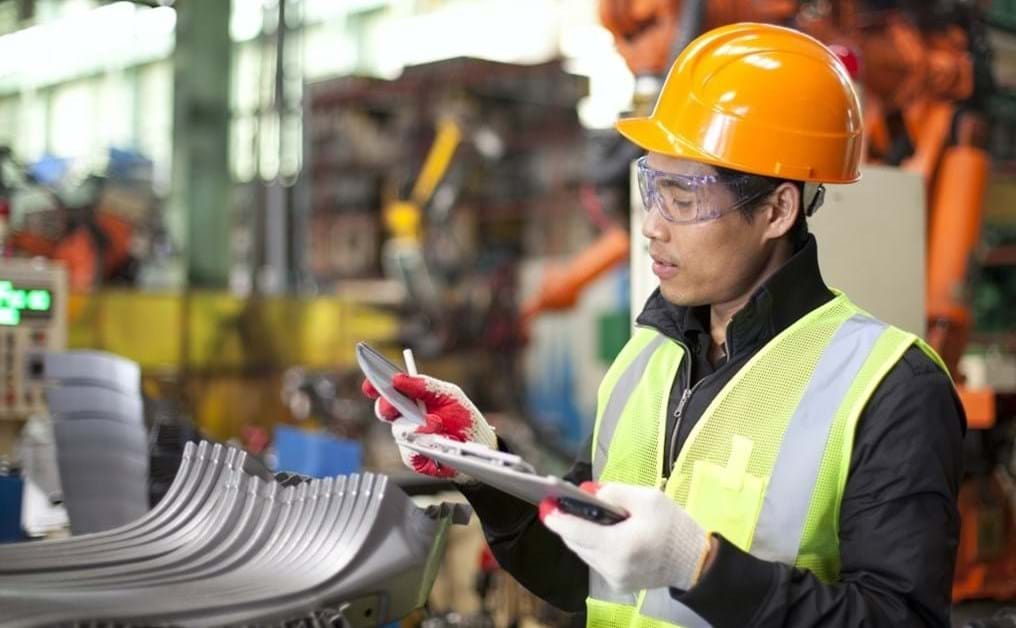
10th October 2019
Chemical and process engineers are key contributors to making working environments safer.
Sharing good practice in this is vital. And so is sharing lessons that have been learned along the way.
That’s why each year we bring leading chemical and process safety experts across Australia and New Zealand together at our conference Hazards Australasia.
This year’s event at the Hilton Brisbane, Australia on 13-14 November 2019 focusses on the theme ‘competence and capability’ and the technical programme features a new panel made up of process safety experts from the regulating bodies across the two regions.
Under the title, Lessons for industry safety cases, the panellists will discuss the importance of sharing lessons from process safety incidents and how the recent Work, Health & Safety review could affect process engineers.
Ahead of this panel discussion, we caught up with some of the panellists to understand some of the challenges and opportunities to improve the safety culture in the process industry in Australasia.
The panellists
From left to right:
- Simon Farrar, Director, Major Hazards & Systems Safety, WorkSafe Victoria
- Tony Hetherington, Head of High Hazards, Energy and Public Safety, WORKSAFE New Zealand
- Meagan McCool, Director, Hazardous Chemical Facilities and Safety Management Audits, SafeWork NSW
- Shoena Messner, Director, Major Hazard Facilities, Workplace Health and Safety Queensland
How do you feel we can ensure those working in process safety and hazard management are best equipped to maintain safety of their facilities?
Simon: Recognise that everyone, from the CEO to the frontline operator, has a role to play; so everyone needs a level of process safety competence and understanding of their role in the system. From authorising a change to reporting unsafe conditions, to the impact of budgeting decisions.
Tony: By making sure process safety and hazard management are at the heart of operational and investment decision making.
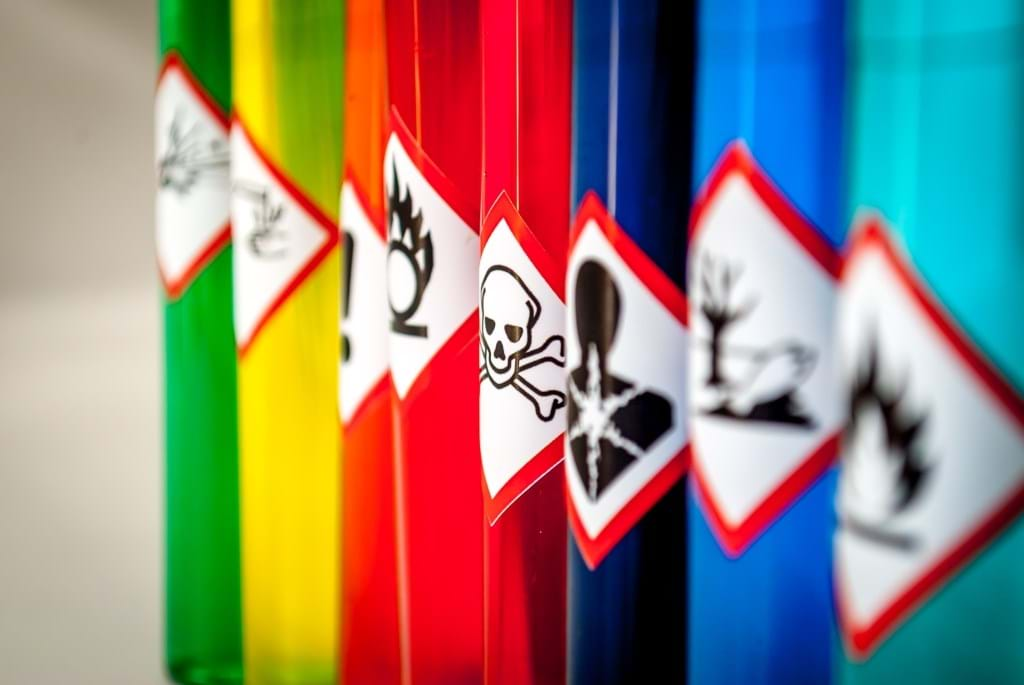
While critical control management is the integral part of risk management that identifies the hazards and risks and provides a selection process for the critical controls to eliminate, prevent, reduce or mitigate the risk to health, safety and property from a potential major incident event (the safety case), it cannot operate without a robust safety management system providing the monitoring insight to ensure the critical controls are working effectively and are consistently applied (the safety case in action).
Shoena: Workers at, or involved in, the management of process facilities must be equipped to recognise danger and act either to return to a safe state or to evacuate themselves and others.
They must have the courage to stand up and speak up. They must have the resources (time, ability and influence) to ensure safety.
Why is it important for chemical and process engineers to continue to discuss safety issues?
Tony: Chemical and process engineers must continue to discuss safety issues because in this field process safety, reliability, resilient production and predictable outputs are all completely interdependent.
An explosion that in whole or part destroys a plant is likely to have tragic consequences for the plant personnel, but the impact is felt far beyond the accident site. Company reputation can be destroyed, shareholder value can be reduced, and the remaining plant may become unviable either because the investment required for repair is not forthcoming or people in the vicinity refuse to accept the risk associated with operations and those dependant on the products may be greatly impacted.
Process safety should be a fundamental element of the whole business risk control strategy. However, generally, process safety is done well, therefore failures are rare and sometimes the importance of maintaining asset integrity, instrumentation or standard operating procedures can be forgotten.
Keeping these issues at the front of the minds of everyone from those who run the plant on a day-to-day basis to those who make strategic investment decisions is essential to maintaining a focus on the issue.
Process safety should be a fundamental element of the whole business risk control strategy.
Meagan: For continuous improvement. While chemical and process engineers are integral to developing the safety case that identifies and selects critical control measures to minimise the risks from potential major incident events, and achieving a major hazard facility (MHF) licence, it is not an end point.
Chemical and process engineers are also integral to the ongoing operation of the safety management system. So often, once a MHF is licensed, the safety management system and/or safety case is handed over to the work, health and safety manager or operations area to manage.
However, chemical and process engineers should continue to play a key and ongoing role in reviewing and assessing the performance standards and indicators to ensure the critical controls are working effectively and consistently applied - not just engaged again following a near miss or for an incident response.
Shoena: Sharing of lessons and solutions helps everyone. A healthy conversation keeps our attention where it is needed and contributes to a positive safety culture.
Furthermore, narrative is almost as powerful as direct experience. We cannot afford to forget the apocryphal stories of the past (Seveso, Flixborough, Bhopal) if we are to avoid repeating them. Unfortunately, most incidents have elements that echo the past.
Simon: We should never stop learning. Learning is crucial in ensuring sustainable safety and much learning happens through discussion.
These can be discussions with people in different roles, having different experiences or different perspectives. Discussions with a range of people will likely lead to new insights, a greater understanding of hazards and how to control them.
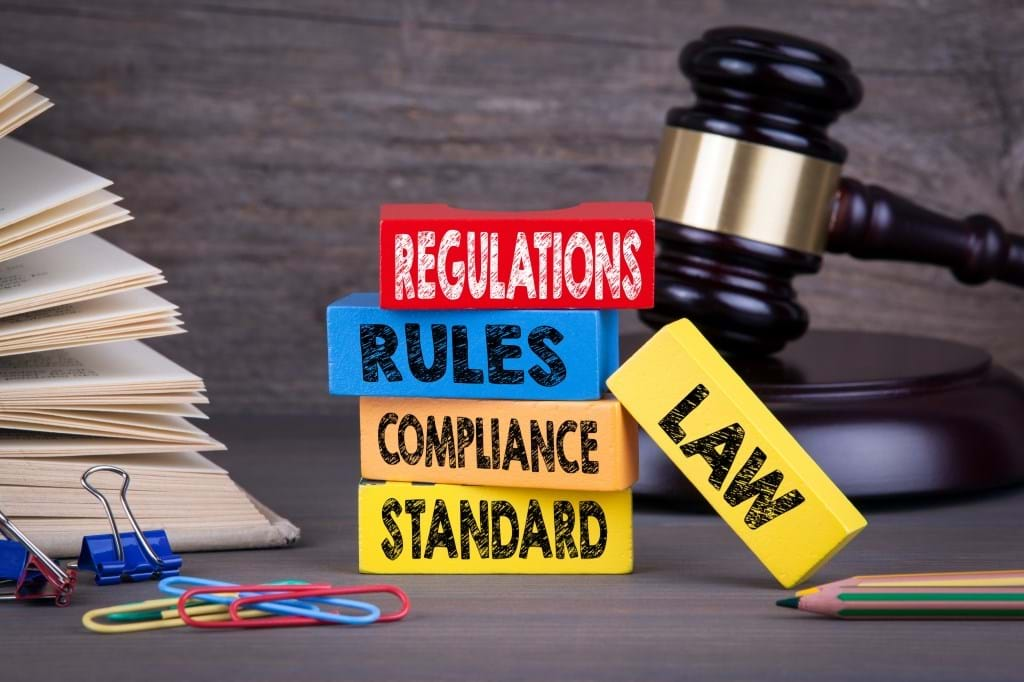
How do you feel chemical and process engineers can help positively influence and improve safety culture across the region and/or the world?
Shoena: By listening, thinking, sharing and caring. Our discipline is about creating products that society either needs or wants. Our facilities are part of the community and the landscape.
We have a duty to our colleagues and those who could be affected by our products or mistakes to make sure that we are as safe as we can be.
The world is full of lessons – we just need to harness and use them.
Simon: Engineers are typically good at analysing problems and finding solutions. These important skills can be used for technical and non-technical matters, of which there are many in high hazard environments.
Engineers can and should also look to understand and translate lessons and good practices from other industries. The world is full of lessons - we just need to harness and use them.
Tony: Within the process industry, chemical and process engineers must ensure that the wider business operators maintain their focus on safe sustainable operation. Helping everyone to understand that safety in almost every industrial operation is dependent upon integrating safety into how processes and procedures are developed is essential to effective health and safety.
Just adding hard hats and safety boots to the worker is the least effective solution. Process safety engineers can help ensure that any operation is safe, resilient, and reliable.
Meagan: Chemical engineers and process engineers can improve safety culture in any industry or region across the world. Swiss cheese modelling, risk modelling, and root cause analysis are the keys to prevention in any industry, not just major hazards facilities or chemicals, and are also essential to incident investigation.
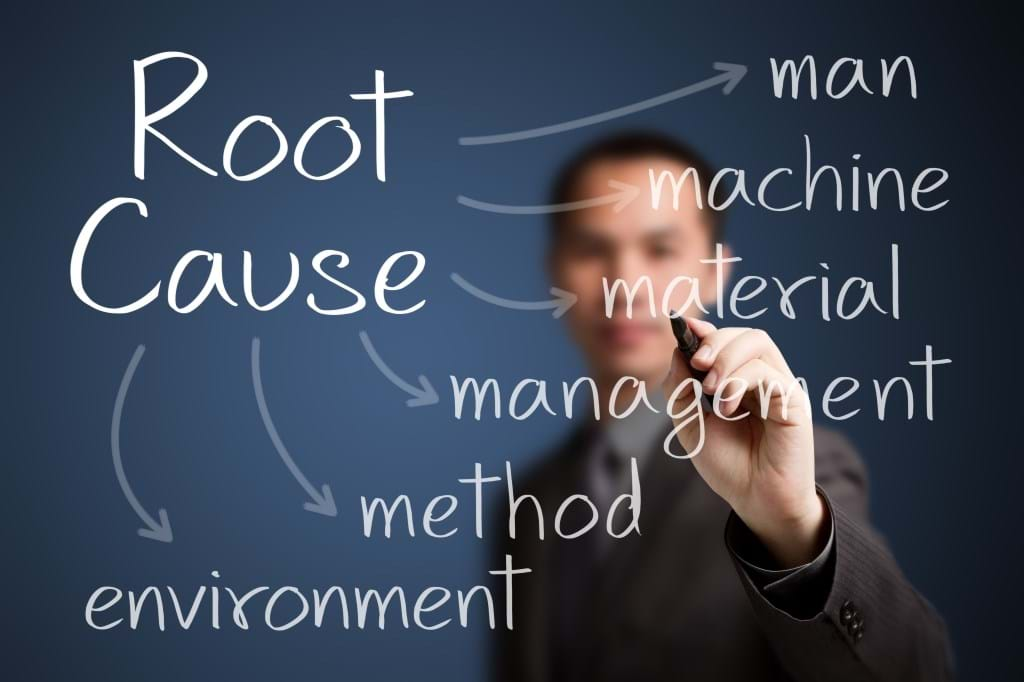
What would be your one key message to facilities regarding process safety?
Meagan: Safety management system performance; including ensuring that chemical and process engineers are part of the ongoing operation of the safety management system.
Shoena: Don’t forget to be afraid. Don’t play the numbers game. You need to be comfortable that you have done everything anyone could have reasonably asked of you to avoid a major incident or environmental harm.
Simon: Be open to and seek information (from others, from incidents, from audits) and always use it to improve.
Tony: Don’t become complacent and assume everything is closed off. Maintain a sense of unease, check that what you think is happening on the plant is actually how it is being operated, especially during the night shift, during repairs and maintenance.
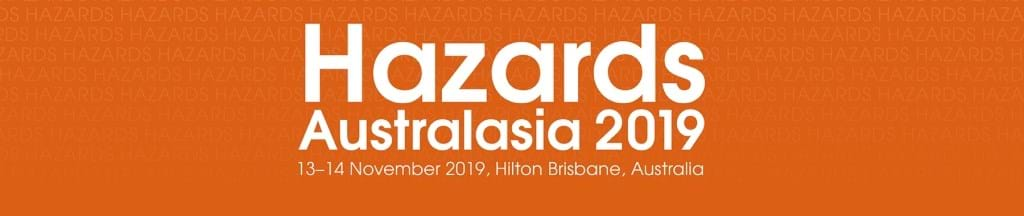