How is COVID-19 impacting process safety management? #Hazards30
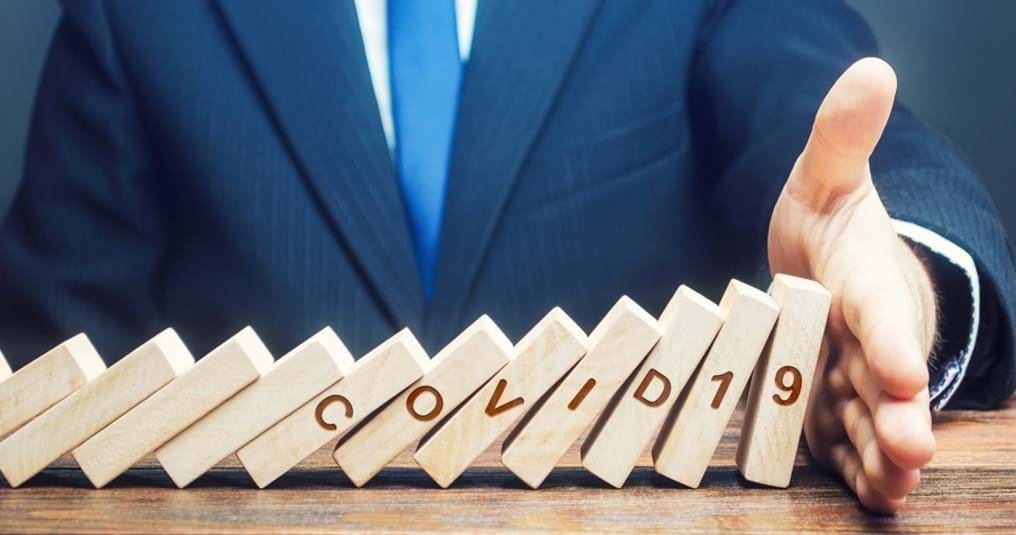
24th November 2020
COVID-19 has turned the world upside down, posing so many challenges for society.
Now it’s more important than ever for us to share good practice and process safety learnings gained so far during this unprecedented time to ensure together we maintain the safety of our businesses and our communities working within, and living by, them.
Like many other organisations, we’ve adapted to fully virtual knowledge-sharing and at our upcoming leading process safety conference Hazards 30 COVID-19 learnings is top of the agenda.
During the event on 26–27 November 2020, presentations will be delivered as part of a live timetable with the opportunity for live Q&A. What’s more, the presentations will be available to view on-demand for up to 30 days afterwards.
Ahead of the event, we caught up with the process safety professionals upon our panel, COVID-19 and Its Impact on Process Safety Management, on day two. Read their thoughts on how COVID-19 has affected process safety in industry and academia, and how process safety skills are key to providing solutions to the current and future crises.
The panellists

Name: Jonathan Carter
Job title and organisation: Risk Engineer, Marsh
Bio: Jonathan Carter is a Risk Engineer with the Insurance Broker and Risk Advisor, Marsh. He runs the Marsh risk engineering hub in Abu Dhabi. He has worked for Marsh for 12 years. Prior to Marsh, Jonathan worked as a Process Safety Specialist Inspector for the UK Health and Safety Executive for 15 years.

Name: Samantha Scruggs
Job title and organisation: Process Safety Technical Authority, BP Azerbaijan-Georgia-Turkey
Bio: Samantha has been with BP for over 15 years, working in Corporate, Upstream, and Downstream roles across the company, and is currently based in Baku, Azerbaijan. Samantha is a graduate of Texas A&M University in the US, with a degree in Chemical Engineering and certificate in Systems (Process) Safety Engineering.

Name: Dr Stewart Behie
Job title and organisation: Interim Director of the Mary Kay O’Connor Process Safety Center and Professor of Practice in the Artie McFerrin Department of Chemical Engineering, Texas A&M University, USA
Bio: Before joining the Texas A&M University, Dr Behie worked at Occidental Oil and Gas Corporation in Texas. Firstly as Manager of Asset Integrity and HES Training and Development where he set up and managed a training programme for engineering and technical graduates, then as Manager of Safety and Process Risk providing risk management guidance and oversight to oxy operations worldwide.
Dr Behie has had extensive experience in health, safety and risk management in the oil and gas industry, and held managerial roles in companies around the world, including in Abu Dhabi, Canada, Qatar and the UK. Behie has bachelor’s, master’s, and doctoral degrees in chemical engineering from the University of Western Ontario, Canada. He is also a registered Professional Engineer in Canada’s provinces Alberta and Newfoundland and has published numerous papers and articles on risk-based decision management, as well as delivered workshops on creating excellence in safety performance and in safety culture maturation.
Tell us how COVID-19 has impacted your organisation, and what response and particular lessons you and your organisation have learned in this time?
Jonathan Carter (JC): As I don't work in a manufacturing organisation, the transition to working remotely from home has been simpler for us at Marsh. We moved to remote working very rapidly in mid-March, and that remains our normal way of working. We continue to engage with clients through teleconferencing. We are now returning to site survey work, carrying out risk assessments of the travel and on-site activity.

Work is also starting on the use of “wearable technology” to support our survey work, minimising the number of people on site while maintaining involvement. We have started to use augmented reality (AR) headsets that are being developed for the oil and gas industry.
These enable dispersed engineering teams to support a single engineer on site, to share information and deliver solutions more rapidly. In our risk survey application, a single risk engineer on site wears the headset, and can involve other engineers to review the condition of the plant and examine critical documents. In this way, travel can be minimized during the pandemic, while still delivering engineering support.
Samantha Scruggs (SS): I’ll actually be speaking about this at a whole session! Please attend the Process Safety & COVID-19 session on 26 November, for a variety of views on the impact of COVID-19 on businesses, with my talk titled, Operating in 2020 – We Did Not See This Coming…
I participated in the Incident Management Team response to COVID-19 for BP in Azerbaijan from March to June 2020, acting as the Planning Session Chief and leading our “London-side Logistics” work. Due to the impact to international travel and supply chain, including the cessation of commercial flights into and out of the country, a significant effort was made to continue safe operations support with essential personnel and services. This included everything from finding viable air routes, ensuring work documentation (visas) were delivered, providing critical worker letters, and securing “Safe Passage”, routes where possible. There was also a workstream dedicated to in-country quarantine and self-isolation housing, including testing, all in service of national requirements and risk management to operational facilities. At times, I felt like a travel agent!
Stewart Behie (SB): In response to the initial COVID-19 outbreak, Texas A&M University (TAMU) shut down its campuses and quickly transitioned from in-person classes to virtual ones. In the fall semester in 2020, around 50% classes were provided as a hybrid model. In this hybrid model, instructors provided face-to-face lectures to the students physically present in their classrooms while live-streaming and video-recording their lectures for the rest of the students.
For face-to-face classes, multiple barriers were introduced. Classes were moved to bigger rooms to allow for greater distance between students, the classrooms were cleaned and disinfected more frequently, a screen was placed between students and instructors, face masks were made mandatory in classrooms and the air filters and air handling systems for all classrooms upgraded to the extent possible (e.g. accommodating for the age and current system in place in the classroom). The measures were designed to ensure campus activities at Texas A&M remained safe.
To accommodate different student needs and motivate student learning, instructors had to employ a mixture of instructional methods and adapt them flexibly. Process safety courses were also adapted to avoid potential risks of COVID-19 and to meet student needs. I taught my first course since joining TAMU in November 2019 in Industrial Safety engineering which was delivered live by Zoom two nights per week for 13 weeks from mid-August to 52 undergraduate students. The quizzes and exams were given online, and monitored by my teaching assistant and I, which required all students to have their computer cameras turned. A course project was assigned to teams comprised of three or four students. A special assignment was given to the students to attend the Mary Kay O’Connor (MKO) International Process Safety Symposium in mid-October and to report on the session discussing the pandemic.
During the first several weeks of the pandemic, buildings on campus were subject to restricted access. For example, access to the JEB Chemical Engineering building required sign in and identification of specific purpose. This restriction was reduced to free access by late summer but the basic COVID-19 protection measures, such as wearing face coverings, were maintained. Some areas remained inaccessible unless prior approval was given. For example, access to the MKO library was by written permission only. In terms of laboratories, initially all lab work was halted. The only research conducted during the initial month of the pandemic was that deemed essential; however, written permission was still required to access labs. During this initial period, all undergraduate research lab work was suspended. As time went on, these restrictions were reduced and access granted on a case by case basis.
Regular updates were provided from the Chancellor’s office and the President’s office on the ongoing impact of the pandemic on TAMU operations and the expectations for the coming months and a COVID dashboard reporting the number of cases in the TAMU community was made available through the TAMU website.
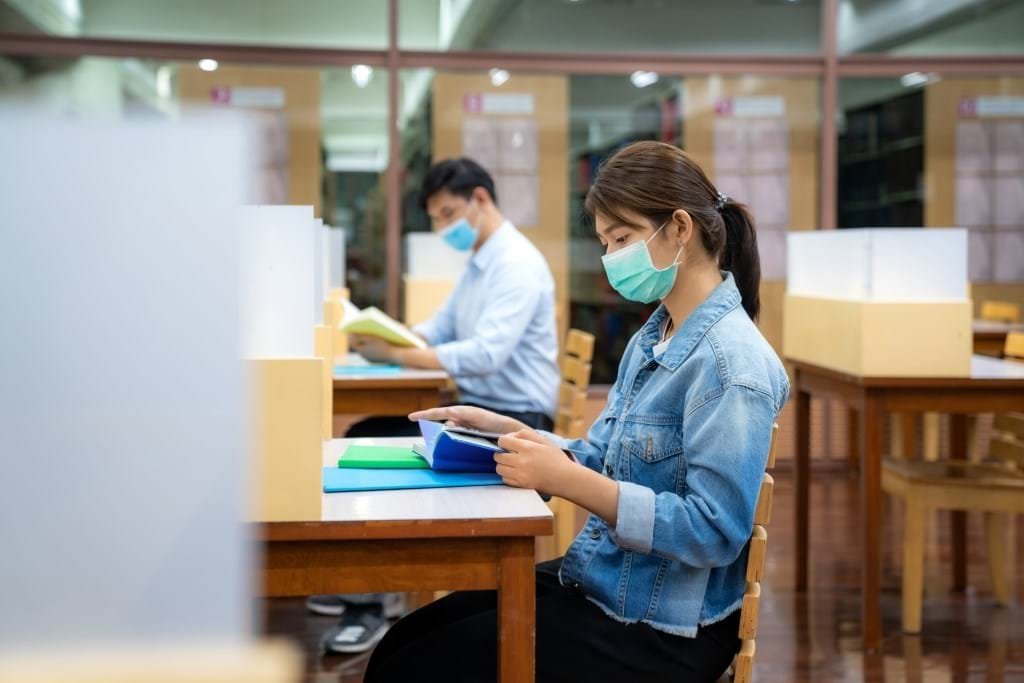
What are the most important skills that process engineers have that are vital in this time of a global response to the pandemic?
JC: Process engineers are used to systematic analysis of potential threats; that’s what we do in a HAZOP. Their role is also to find solutions and to minimise risk at an optimum cost. The effective response to COVID-19, to maintain safe and effective operation of process plants in times of a pandemic, relies on the effective use of these skills that process engineers have trained in and applied for their whole careers.
SS: As process safety engineers, we are trained to look at the whole system, take all the disparate information we have, and then tell a story with it. We then reshape our insights and response as new context come in, and find ways to make things better, safer, more efficient, and more effective. It feels like that’s what the world has been doing since the beginning of the year – both in trying to understand and respond to the pandemic. I believe we, as a community, are uniquely suited to translating and integrating all this information in both our home and work lives.
SB: A process engineer has a number of important skills that can be drawn on to understand and help others navigate through a pandemic. These include:
- Understanding the concepts of layers of protection and defence in depth. This understanding of the need to put preventative measures in place and more importantly to assess and monitor them over time to ensure that they are maintained so that the credit taken for their effectiveness is not overstated.
- Understanding the risk assessment process allows the process engineer to develop event scenarios of potential upset conditions and to logically postulate the likely impact and the frequency of occurrence. The probability estimate is based on the number of protection layers that are in place or that can be readily added to reduce probability of occurrence if needed. This rigor of the risk assessment process starting with the first question of, “what can go wrong?”, allows the risk engineer to maintain situational awareness of the impact of critical impact scenarios.
- Understanding the importance of planning and the need to prepare detailed plans to assess the impact of major upsets that can bring an organisation to its knees both process related and non-process related. This process includes the development of robust recovery plans for each scenario, which in total form the corporation’s Business Continuity Management Plan. A plan to prepare for, and recover from, a pandemic is one of the upset scenarios that must be included in an overall Business Continuity Management Plan. Planning is key. To quote Harvey Mackay, “If you fail to plan, then you plan to fail”.
- Understanding and applying the concepts of risk-based decision making and management to assist in providing guidance to improve the outcome of critical technical decisions through the assessment of the risks associated with the relevant event scenarios that are germane to critical decisions.
- Embarking on a continual improvement process of enhanced learning to stay abreast of the changes in the operating environment and the skills set that are needed to navigate these changes.
How do you think the process industry may have to adapt to enable a more sustainable future post-pandemic?
JC: The pandemic has demonstrated the need for resilience to be built into the ways we work.
As we plan, develop and innovate, resilience needs to be built in to the processes and businesses we are building. If we add pandemic risk and plan our response to it in this way, we can ensure that our processes and businesses will be able to continue in the event of the foreseeable, but remote, disruptions and interruptions from the wider world.
SS: Earlier this year, bp announced its new purpose, net zero ambition and aims, and its determination to reimagine energy and reinvent bp. Sustainability is a critical foundation of bp’s strategy, which link’s to bp’s purpose and net zero ambition, as well as our wider approach to environmental and social issues. We have established three clear focus areas:
- Get to net zero;
- Improve people’s lives; and
- Care for our planet.
Each of these include prioritised themes linked to the UN Sustainable Development Goals. This will be supported by setting clear aims and objectives, embedding sustainability within our DNA and intensifying the search for external collaborations and partnerships that can help us to drive progress, provide skills we may not have, and help us to shape the future together.
Some of our steps in sustainability in 2020 include launching our updated human rights policy with a focus on modern slavery and the rights of vulnerable groups and pledging not to undertake new oil and gas exploration or production activities within natural, cultural or mixed UNESCO World Heritage sites.
Our company is dedicated to delivering these plans, and believes it is even more critical post-pandemic.
SB: The lessons learned from the current COVID-19 pandemic offers a unique opportunity for the process industry to learn and to develop plans to prepare for and recover from the next pandemic. There will be a next pandemic – it is a matter of “when” not “if”. This pandemic preparation should be developed as a part of an overall Business Continuity Management Plan and include other major upset conditions that have the potential to bring a company to its knees.
The key components of a Pandemic Preparation Plan should include:
- The development and monitoring of leading indicators metrics to provide an early identification of a pandemic threat and the associated response mechanisms by level of threat (emergency support groups / crisis management team). The plan needs to also outline the key actions that need to be taken to stay ahead of the threat including health and safety bow ties.
- The rigorous, predetermined protocols required to manage and control personnel access to operating plants that are deemed essential infrastructure and must remain in operation, and the enforcement measures that will be taken for wilful violations of the protocols.
- Communication plans given by senior management that sort the facts from the fiction and provide regular updates to staff and family members through the pandemic to avoid the tendency to declare victory when none is in sight. If not in place already, establish regular town-hall type meetings to enhance communications at all levels of the organisation and to address what measures are in place to deal with upset conditions.
- The identification of partnerships in each plant region both public and private with a view to fostering confidence in the workforce and the public that things are under control.
- Ongoing identification of the layers of protection (health, security and so on) that have been put in place to control the pandemic and prevent its spread.
- Identifying plans that will be used to transition through various phases of a pandemic with a focus on determining the triggers that signals when a plant or company has progressed to the recovery stage.
- A ‘Back to Work’ plan needs to be prepared that outlines the stages of the movement of staff back to the workplace work and to explain the rationale behind the plan.
Operating plants are much more effective and functional when staff are working face-to-face and interacting on an ongoing basis. Despite this reality, however, industry will have to rationalise and reassess the overall workforce profile and determine what support functions can be performed effectively remotely and have the flexibility to try different models. In addition, industry needs to reassess the level of operating staff needed to effectively and safety operate plants as well as the employee/contractor mix and be prepared to make changes that reflect changing circumstances. In this regard, there will be a push by industry to assess technologies that move in the direction of remote operations and control to improve overall efficiency and effectiveness. This trend will include the use of drones and digital twins to plan turnarounds and shutdowns more effectively.
What would be your one key message to process safety professionals as the pandemic continues?
JC: The key message is the simplistic “stay safe”. But to expand on that, carry on using the tools and skills that you have always used to deliver safety and process safety, identifying the causes of risk, assessing likelihood and consequences, specifying barriers and assuring their reliability, adding the additional context of the risk of communicable diseases. In this way, you will continue to support the delivery of a safe and healthy workplace.
SS: “To take care of others, start by taking care of yourself.” Mental health is such an important thing to protect, and the past year has been one of the most challenging that some have faced. With the blurring of working from home, or “sleeping at the office” as some have said, the balance that we once had to recharge is missing. It has been absolutely critical for me to reset, if I’m honest, a few times over the last nine months. We aren’t good to the people we love, or the people we work with, if we’re not good with ourselves.
SB: The lessons learned from COVID-19 offers a unique opportunity for the process safety industry to learn from the past pandemics and to lead the effort in your organisation to develop and implement plans to prepare for and recover from the next pandemic. The devil is in the details. Process safety engineers need to treat pandemics as a major hazard and lead the development of detailed plans and protocols to conduct risk assessments of scenarios to assess the impacts at the various stages of pandemic development. These assessments will become components of the overall corporate risk profile along with major loss of primary containment (LOPC) events.
A significant component of these plans is the preparation of emergency response plans to address the issues as they develop from initial identification of a pandemic threat through to the final recovery stage. The identification of the triggers that signal the transition through the various phases of the pandemic response.
Process engineers working in process plants, particularly those who operations are deemed “essential services”, must ensure that all the requirements of the plan to maintain operations are met by all personnel, both company staff and contractors. This includes testing, basic hygiene programmes, staying home if symptoms develop, conducting ongoing risk assessments to confirm conformation to all requirements and implementing consequence plans should violations occur. The requirement is 100% compliance – no exceptions. To facilitate this effort, detailed checklists should be prepared and used to capture the results of the ongoing plant tours and assessments.