Day 148: Five every day products and the chemical engineering that goes into them
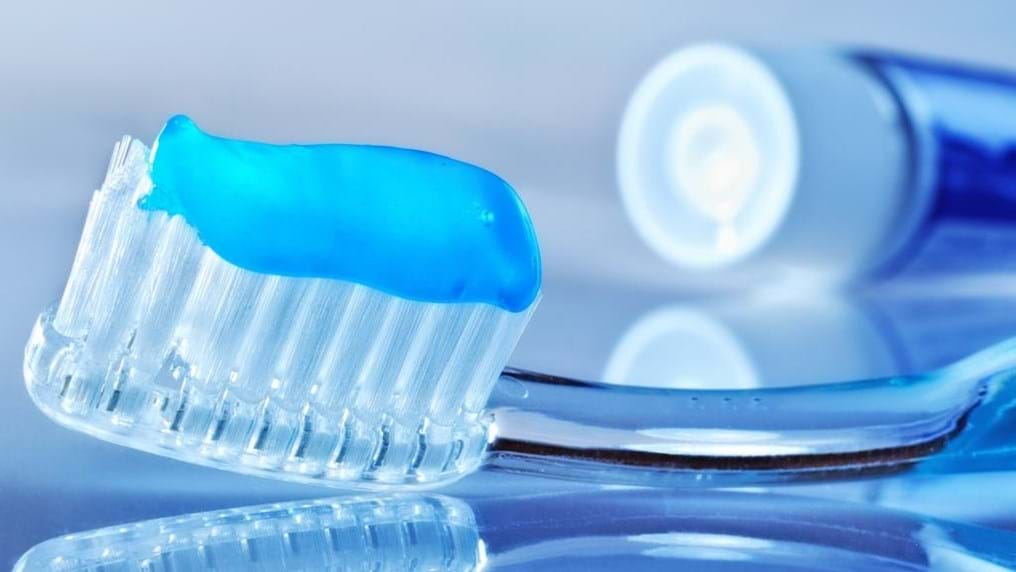
22nd October 2014
Author: Geoff Maitland, IChemE President 2014–2015.
Chemical engineering is often described as process engineering. But many chemical engineers work as product engineers within the fast moving consumer goods market.
The products that we buy and use every day, and often take for granted, have been chemically engineered so that they fulfil their required function.
And as you know, the best way to explain something is by way of example. That's why I've compiled a list of products explaining the science and engineering that goes into them.
The products are also a great way to introduce young people to a potential career in chemical engineering .
1. Hairspray

This hair care product is incorporated into many people's morning routines. Both men and women want to achieve a desired hairstyle. So it is important that hairspray is designed to provide a strong hold that lasts throughout the day.
Hairspray consists of complex polymers that have the ability to form invisible bonds across our hair's fibre intersection.
The choice of these complex polymers in hairspray directly relates to consumer need, so vinyl acetate is used to ensure strong hold and, in addition, is resistant to humidity.
Hairspray is usually packaged in an aerosol can powered by a pressurised gas - dimethyl ether. This gas acts as a propellant within the aerosol and is boiled away when the nozzle is pushed down. The rest of the ingredients are then propelled out of the can in the form of a fine mist.
Hairspray is produced in a batch process in large tanks of around 9,000 L where the ingredients are mixed by large turbine blades - the main base of this product consists of water and a denatured alcohol.
The other ingredients that are added to perform specific functions include perfume oil (pretty self-explanatory), amino methyl propanol which controls the acidity of the product, cyclopentasiloxane which acts as a thickener, lubricant and water repellent to give hairspray its 'silky feel', and borate esters that prevent the aerosol can from rusting.
2. Toilet Paper

Every household will need its supply of toilet paper and so this makes the product a must-buy consumer product.
Toilet paper can be made from either 'virgin' or new paper (formed of chipped wood) or from recycled paper.
The other materials used in its manufacture include water, chemicals for breaking down the raw materials into usable fibres and bleaches.
When the raw materials include recycled paper, the batch process starts by mixing all the different types of paper and then removing the ink by injecting the pulp with air - the ink particles can then be skimmed off as they rise to the top of the pulp mixture.
If the feed into the process is 'virgin' or new paper, the chipped wood is cooked within a pressure cooker in order to evaporate some of the excess water and reduce the wood into pulp.
The pulp mixture, whether from 'virgin' or recycled paper having now been cleaned, is passed through some heated rollers to reduce the moisture content to approximately five per cent so that it is ready for bleaching. Before bleaching, the mixture is chopped back up into pulp.
Once bleached, the wet pulp passes through a high temperature dryer and is rolled into paper which is one ply thick. From this point, the paper can be embossed with a pattern which actually increases its thickness.
Automated machines then do the final job of unwinding, cutting and then rewinding the paper onto cardboard tubing. Rolls of toilet paper are then cut and wrapped into the final product that we see line the shelves of the supermarkets.
3. Deodorant

Almost everyone uses deodorant at different times throughout the day and usually they are delivered to the consumer as either roll-on deodorants, sticks or aerosol sprays, to be applied usually to the underarm area.
Deodorant is designed to prevent body odour, and antiperspirant deodorants are designed to prevent sweating - a subtle difference but the desired outcome is to keep the individual smelling fresh.
Deodorants are typically manufactured in a batch process within high shear mixers that have a volume capacity approaching 2,000 L - the formulation and combination of ingredients really depends on what form the product is going to be delivered to the consumer.
Solvents or silicones are mixed with the powder ingredients such as cetyl alcohol into the oil phase within the mixer. The active ingredient is prepared separately in an aqueous, dispersed phase.
Both the oil phase and dispersed phase are combined and this forms an emulsion. If the end product is a delivered as a stick or roll-on, then gelling agents or polymers are added. Otherwise, perfume/fragrance is the next ingredient before the product is cooled and then poured into containers to be packaged.
The active ingredients in deodorant differ from that of antiperspirants because of the different ways they inhibit odour. Aluminium based compounds are usually the active ingredients for antiperspirants, with aluminum zirconium tetrachlorohydrex glycine being the most commonly used.
Batch testing the products for safety and efficacy is an important part of the process, as products often land on our shelves with labels that state such things as '48 hour protection' or 'contains aloe vera'. Manufacturers need to make sure that their products are safe, functional and contain exactly what it says on the container.
4. Detergent/washing powder

Detergent or washing powder is a staple product that's found within most households in order to clean clothes, linen and other textiles. When the powder is dissolved in water i.e. within a washing machine, it aids the removal of dirt from a textile surface.
Detergent powder can be produced in either a batch or continuous process, with the larger manufacturers favouring the continuous process, also known as the agglomeration process.
Detergents are based on the surface active ingredient or surfactant. Surfactants consist of hydrocarbon chain and a hydrophilic ionic or non-iconic group, both of which perform a specific function.
The hydrocarbon chain part of the surfactant molecule attaches itself to dirt and the hydrophilic end attaches itself to water. This means that the dirt is chemically removed by the hydrocarbon chain into the water. The most common surfactants used in industry are anionic and usually come in the form of water-soluble sodium salts.
Enzymes and perfumes are other ingredients of detergent. The enzymes are present to break down stains and the perfumes are added to ensure that the laundry smells nice, and covers the chemical smell of the detergent.
The agglomeration process starts with the dry ingredients being fed into an agglomerator where blades mix the material into a fine consistency. Liquid ingredients are then added to the mix via spray nozzles directly into the agglomerator. This reaction produces heat which leads to the formation of a hot, viscous liquid.
Once the liquid exits the agglomerator, hot air blowers are applied and the detergent collects on a drying belts. This is then pulverized and pushed through sizing screens (to avoid large lumps of powder) to form the detergent/washing powder product that then goes on to be packaged.
If the detergent is a liquid product, the powder is simply blended with a solution of water and solubilizers - the solubilizers aid the mixing of the detergent and water.
5. Toothpaste

Toothpaste has become an essential product, often complimented with the use mouthwash and dental floss.
An important ingredient of toothpaste is fluoride. Fluoride acts as the active ingredient - it prevents decay and the formation of cavities by increasing the strength of teeth. Sodium fluoride is the most common fluoride compound used in the manufacture of toothpaste.
Other important ingredients of toothpaste include: binders, which acts as a thickener; abrasives, which loosen the plaque from the teeth; foaming agents (surfactants); which, which retain water; flavours; colourants and sweeteners.
Toothpaste manufacture is a batch process, where ingredients are weighed before mixing. Each batch can produce an equivalent of 10,000 tubes of toothpaste.
An important feature of some toothpastes are the different coloured stripes. Artificial dyes are added to a batch to change its colour. Essential oils are then used to add these colours (which often attribute to a different flavour) to the product at the packaging stage.
The final product is filled into tubes, with the use of automated equipment and pumps and it is at this stage that the product is tested for safety and efficacy.
++++++++++++++++++++++++++++++++++++++++++++++++++++++++++++++++++
This blog is perhaps longer than my other posts, but it just goes to show how much engineering and science goes into making the products that we use every day - and that certainly is something chemical engineers should be proud of.
ChemEng365 blog
Geoff Maitland launched this blog during his IChemE presidency in 2014. ChemEng365 features 365 chemical engineering successes and achievements throughout his year-long presidency.