A breath of fresh air (Day 351)
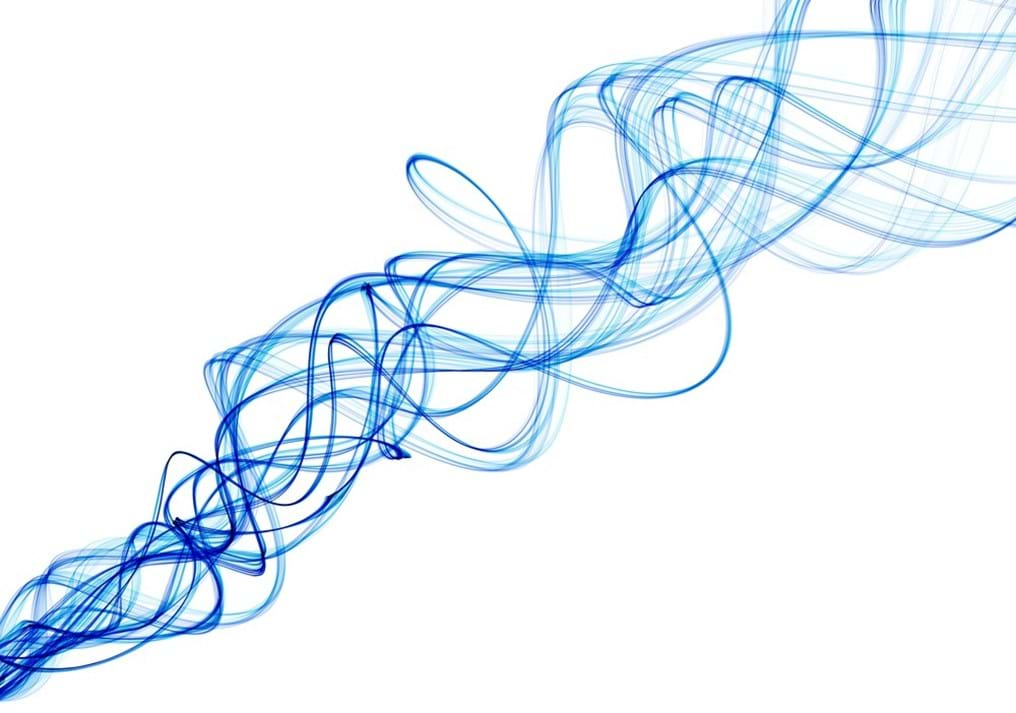
13th May 2015
Chemical engineering has to be one of the most creative of all professions. We look for opportunities in everything, even in the air that surrounds us.
In the early 20th century, Carl von Linde pioneered the process of air separation, splitting air into its pure components. He developed a technique to obtain pure oxygen and nitrogen by means of fractional distillation from liquefied air.
Since then, air separation has been applied to many products we use every day. In February, I attended an IChemE event at the University of Surrey. During the event, I met Jama Salimov, an Advanced Process Control Engineer at Air Products. Jama was keen to shine a light on his work in air separation and ensure that we all understand its many applications.
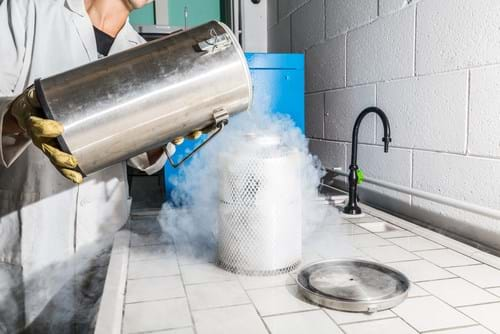
Air separation typically separates air into its primary components – nitrogen and oxygen. However, it can also isolate some of the more rare parts of the air such as argon.
The products of air separation have a wide variety of uses in our everyday lives. Many of us use them without even realising it – and Jama was keen to tell me all about them.
At first glance, the process of air separation seems very simple. It follows the same principles as a fridge in your house. The air is cleaned of impurities, pressurised, cooled down and distilled into its pure components at cryogenic temperatures (below 150 oC). See the picture below for more details on how the process works:
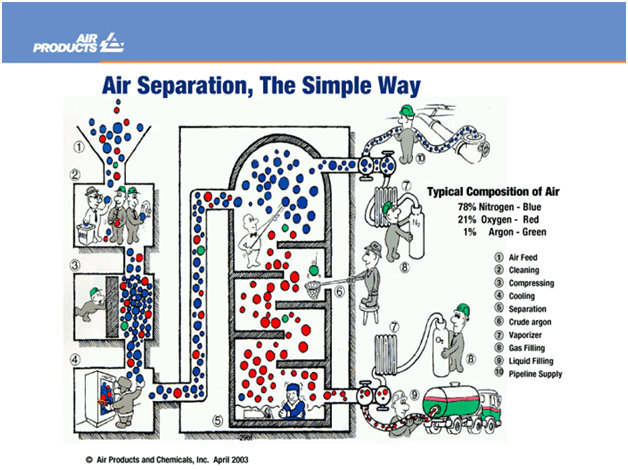
Air is separated in large chemical plants, where impurities are removed. This is normally done by either Pressure Swing Adsorption (PSA) or Temperature Swing Adsorption (TSA). The filtered air is then pressurised to around 40 bar.
It is then chilled in a distillation column where the air is separated into its component parts using a packed column, in which the nitrogen moves to the top of the column, then the argon to the side and oxygen to the bottom.
Air Products process the separated air and supply a wide range of industries and businesses. Because of the vast applications of their 'air products' they have a very varied range of clients; from refineries to schools and garages to restaurants.
Jama told me about some of the direct uses of air products, some common and some a bit more unusual!
Separated air is big business in the food industry, for example in food packaging and freezing.
When meat is packed into plastic packaging, the oxygen is removed and then the package is pressurised using inert separated gases. This technique is called MAP (Modified Atmosphere Packaging), which aims to extend shelf-life and is discussed in my earlier blog ‘Put a label on it to reduce food waste’.
Liquid nitrogen is also used by food producers to help preserve food. For example it can be used to flash-freeze meat to low temperatures (eg -197 oC). This not only improves shelf-life, but also preserves the meat quality as it reduces the formation of ice crystals.
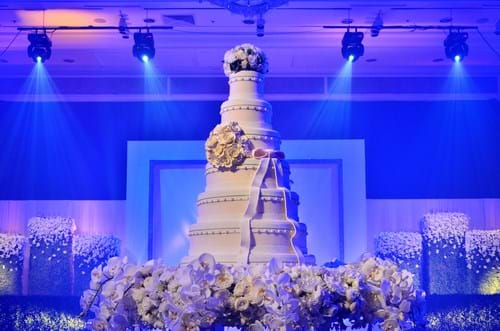
Another application of air products is the use of oxygen, instead of air, in furnaces for metal production. Oxygen can be used to maximise the efficiency in cement manufacture and steel production, meaning less fuel is used so any large equipment could be made smaller.
Air separation is also important in healthcare. Think of the cylinders of gas used for people who need oxygen; this gas is produced using separation technology.
Liquid helium, separated from air, is used to cool down the super-conductive magnets in MRI machines. The electromagnetic coil could get very hot and liquid helium is the air product cold enough to cool this.
Jama is correct in saying that this is a really interesting and fun field for chemical engineers. The wide variety of applications this technology offers are a breath of fresh air! This is another great example of how chemical engineering matters.